Dry goods: Experience sharing of 3D printing data model
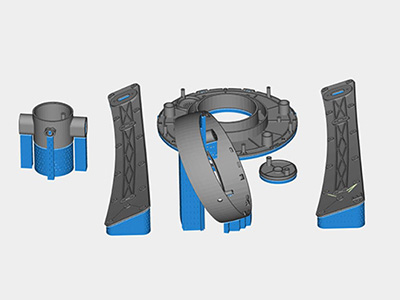
In the era of big data, data has penetrated into every industry and business function and become an important production factor. Our 3D printing is also part of this ocean of data. 3D printing cannot do without data model. Where does the data come from? What can we do to make these data models easy to print and nearly perfect and still achieve our printing goals? This issue small make up to take you a crack!
First of all, what is a data model? Data model refers to the form expressed in the design scheme, positive drawing (original drawing), sketch, technical description and other technical drawings of an engineering or product by computer software, scanning, surveying and mapping or other means, which is constructed into a digital model that can be used for design and subsequent processing work.
So, what are the formats of 3D printing data models? In general, the most commonly used is STL, of course, can also provide OBJ, STEP, IGES and other common formats for conversion. STL is a three-dimensional surface data file format. Its basic principle is to use small triangular surface to edit the free-form surface of three-dimensional entity to describe the geometric information, and does not support the information such as color and material.
Data model requirements
(1) The object model must be closed
Commonly referred to as “watertight”, it can be checked with the help of some software, such as STL detection for 3DS Max, Magics repair wizard, etc.
(2) The object needs thickness
In all kinds of software, the surface is ideal without wall thickness, but there is no thing without wall thickness in reality, so it is not possible to form an unclosed model surrounded by several surfaces in modeling.
(3) The object model must be manifold
For a complete definition of manifolds, refer to the mathematical definitions. For our purposes, a grid data is nonmanifold if there are multiple faces sharing an edge.
(4) The correct normal direction
All plane normals in the model need to point in the right direction. If your model contains the wrong normal direction, the printer will not be able to tell whether it is inside or outside the model.
(5) Minimum thickness of the object model
The wall thickness of the print model should take into account the minimum wall thickness the printer can print. Otherwise, there will be failed or incorrect models and the minimum wall thickness will vary depending on the 3D printer.
(6) Delete redundant geometric shapes
If some reference points, lines, or surfaces during modeling also include hidden geometries that are not deleted when the modeling is complete, the redundant geometries need to be deleted.
(7) Delete duplicate dough
In modeling, duplicate faces will be generated when two faces are superimposed, and the duplicate faces need to be deleted.
Data model acquisition
- Object mapping
According to the structure characteristics of the object, systematic analysis and measurement are carried out to determine the basic structure and surface type of the model and establish a data model that can be 3D-printed. This method is suitable for objects with regular structure comparison.
- Three-dimensional inversion
According to the structure characteristics of the object, the object contour structure and color scanning is carried out to obtain the spatial coordinates of the object surface, and the three-dimensional information of the object is converted into computer data. The three-dimensional scanning technology can realize the non-contact measurement, and has the characteristics of fast speed and high precision. This method is suitable for objects with complex structure.
- Two-dimensional drawings/pictures/photos /CT/MRI
Establish a data model based on 2d drawings/pictures/photographs /CT/MRI.
Data model repair
- Repair STL model files
There may be some problems with THE STL model, which may lead to quality problems in the printing process. By repairing the shell, holes, gaps, bad edges and triangular pieces of the model, the printing success rate can be improved.
- Repair the scanned data
Scanning data are generally 3d point cloud data or STL format surface files, and the scanning data are repaired by surface subtraction, repair, smooth, surface reconstruction, etc., to obtain the original data of scanned objects.
Data model slice
- Optimize the placement mode, which can improve the printing quality of the model and reduce the production cost of the model.
- Pulling the shell can reduce the weight of the model, reduce the cost of the model, and add certain topological structure if there are special requirements.
- Adding z-axis compensation can ensure the dimensional deviation of model data printing to a certain extent, and reasonably add support, which can improve the success rate of model making. Of course, different printer slices have different requirements, which should be handled according to the actual situation.