Take you to understand the genius of metal 3D printing
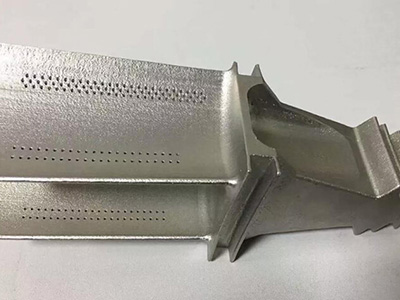
First of all, I would like to introduce the technological process of metal 3D printing and the pictures of the finished products.
Metal 3D printing is known as the weathervane of the development of 3D printing industry. The development of 3D printing industry largely depends on the development of metal printing technology. Metal printing technology has many advantages that traditional processing technology (such as CNC) does not have. It is believed that more and more new materials will be used in 3D printing in the future to provide greater convenience for product printing and the production of complex parts.
Introduction to metal 3D printing
Metal 3D printing is usually realized by using digital technology material printer. It is often used in mold manufacturing, industrial design and other fields to make models, and then gradually used in the direct manufacturing of some products. There are already parts printed by using this technology. The technology has applications in jewelry, footwear, industrial design, construction, engineering and construction (AEC), automotive, aerospace, dental and medical industries, education, geographic information systems, civil engineering, firearms, and other fields. Today, What Prindream will share with you is the PRINCIPLE of 3D printing, mainly introduces metal 3D printing technology.
Detailed description of SLM metal 3D printing process
SLM, or selective laser melting molding technology, is the most common technology in metal 3D printing molding at present. It adopts fine focusing spot fast melting preset metal powder to directly obtain any shape and parts with complete metallurgical combination, and the resulting production density can reach more than 99%.
Laser galvanometer system is one of the key technologies of SLM. The following is the working diagram of THE galvanometer system of SLM Solution Company:
Laser Emission
Laser transmission
Scanning galvanometer
Laser scanning melting
The melting process of metal powder
In the process of metal 3D printing, support materials need to be printed because the parts are usually complex. After the parts are finished, the support needs to be removed and the surface of the parts is treated.
Take out the parts
Remove the support
Post-polishing treatment
The finished product to show
Metal 3D printing can effectively improve the design freedom of industrial parts, molds and other products, and produce crystal structures with complex shapes. Traditional metal casting technology is often difficult to achieve good results, but metal 3D printing has a significant advantage in product design and molding.
On the whole, metal 3D printing can not only give designers greater freedom to give play to their own ideas, but also save a lot of costs in product manufacturing, reduce product weight and enhance product stability. As far as the application of metal 3D printing in the aerospace field is concerned, the weight of aircraft can be reduced and the fuel cost of aircraft can be further reduced by installing metal 3D printed seat belt buckle with honeycomb incision and other parts.
In fact, in addition to the advantages of shortening product development cycle and improving material utilization rate, metal 3D printing is particularly noteworthy for its advantages in improving the flexibility of product casting. With the help of metal 3D printing technology, industrial products with complex shape and structure and high precision requirements can better meet the actual needs in the casting process, and unnecessary technological process can also be simplified, which is efficient and reasonable.