3D printing makes manufacturing “lightweight”
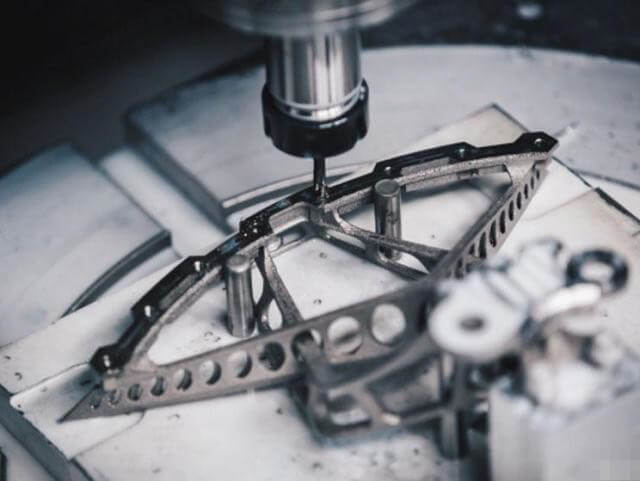
HRE, a Californian wheel manufacturer, has invented a 3D-printed wheel designed for the McLaren P1, foreign media reported.This wheels make the vehicle run faster by reducing its weight
This is HRE’s second-generation 3D-printed concept wheel. The wheel consists of a carbon fiber gun barrel and titanium alloy spokes. And each wheel weighs about 9kg,the McLaren P1 will accelerate faster with this lightweight wheel.
In the manufacturing process of the supercar wheel, HRE adopts two 3D printing technologies. One is the direct metal laser melting process, which uses the laser to melt the ultrafine titanium alloy powder and build the titanium alloy molten layer, layer by layer to create the fine particle layer and form the finished wheel.The other is an electron-beam smelting process, in which a beam of electrons is heated to melt the new metal in a vacuum vessel.
In addition, when ordering HRE 3D-printed wheels, users can choose different colors and primers to customize the operation. These wheels are all hand-made and take a long time to make but the process is very delicate.The 3D printing technology uses titanium alloy, which ensures the strength of parts and makes it possible to customize the development of wheels in the future.
In the automotive sector, 3D printing is used not only to make wheels, but also for other lightweight, customised parts or moulds.Ford Has 3D printing labs that make buttons, knobs, air intakes and hood parts for cars.Bugatti also has an eight-piston brake caliper made by 3D printing, while Mercedes-Benz and Porsche are also using 3D printing to make metal parts for older models.
There are three ways to realize lightweight: First is the optimization design and application of materials;The second is the optimal design of product structure;Third is the development and application of advanced manufacturing technology.The three complement each other to realize the lightweight manufacturing of the final product, among which the optimized design of product structure and material has a vast space for research and development.
Lightweight materials can be used to reduce the weight of the product and improve the comprehensive performance of the product.Material lightening refers to the method of weight reduction through the use of lightweight metal and non-metallic materials on the premise of meeting the requirements of mechanical properties.
In the current lightweight materials, steel and iron still play a dominant role, but the proportion of steel and iron material decreases year by year, and the proportion of aluminum alloy, titanium alloy, magnesium alloy, engineering plastics, composite materials and other materials increases gradually.These materials are especially widely used in the field of automobile manufacturing, among which aluminum alloy is the most widely used and the most common lightweight 3D printing material for automobiles at present.Another common lightweight 3D printing metal material is titanium alloy.The main advantages of titanium alloys are low density, high strength density ratio and excellent corrosion resistance, as well as high strength even at temperatures up to 500°C.Compared with steel, aluminum alloy and magnesium alloy, the main disadvantage of titanium alloy used in automobile is high cost. However, its application in other aspects of automobile has the potential of lightweight, which can be used in manufacturing components such as suspension spring and exhaust system.
In addition to alloys, a number of new lightweight materials have emerged in recent years, including carbon fiber.Studies have shown that if the strength of reliable carbon fiber instead of steel, the quality of the body, chassis will be reduced by 40%-60%, the lightweight effect is evident.
At present, carbon fiber cannot be directly used for 3D printing. It is usually used as reinforcing material, including staple fiber reinforcement based on laser sintering and long fiber reinforcement based on FDM.Embedding carbon fibers in conventional materials can make components dozens of times stronger, with a strength-to-weight ratio even greater than that of many metals.This manufacturing process is more similar to the new material design, so it has a wide range of applications in lightweight.Another lightweight material is engineering plastics, which are used to make automotive interiors, appliances, intake manifolds, control panels and other components, both for prototype verification and for direct manufacture of final functional components.
The use of lightweight materials must be combined with product design and manufacturing process, only in this way can the effective purpose be achieved.The development of new technology suitable for lightweight materials can not only accelerate the application of new materials in automobiles, but also reduce the cost of materials, which is conducive to the expansion of applications.And 3D printing layer upon layer stacking technology principle, no fear of design complexity, can effectively optimize the structure of parts, reduce the loss of material waste, reduce weight, reduce stress concentration, increase the service life.Even though 3D printing can produce only a limited number of materials directly, there doesn’t seem to be much resistance to making lightweight materials directly.
In addition to the heavy use of composites and light alloys, the integrated manufacturing process for new materials will significantly reduce the number of body parts and significantly change the way car bodies are designed, according to projections from the automotive industry.
At present, mature 3D printing technology and materials have attracted the attention of many automobile manufacturers. Volkswagen, Ford, BMW and other automobile manufacturers have set up advanced manufacturing centers including additive manufacturing, which undoubtedly brings more opportunities for lightweight manufacturing of automobiles.